In the summer of 2019, the construction project was staffed, and during the summer and autumn of 2019 the project focused on planning and procurement.
The first shovel of soil was turned on March 23, 2020 and during the spring and summer, groundwork was carried out, as well as casting of baseplates and connection preparations.
The installation of the pyrolysis plant took place in the spring of 2021 followed by the construction of the office and workshop space. The plant was put into operation during the autumn and on December 7, 2021, the factory was inaugurated.
About the pyrolysis plant
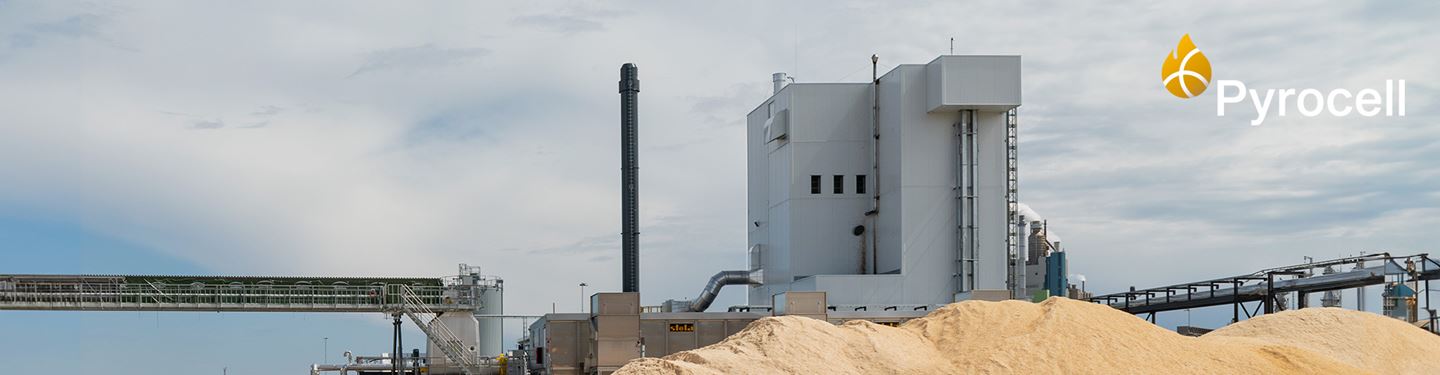
The Pyrolysis plant
Sawdust from Setra's sawmill in Kastet is used as raw material to produce a pyrolysis oil, which then constitutes a renewable raw material in the production of biofuel at Preem's refinery in Lysekil.
Process description
- Sawdust from the nearby sawmill, and other plants, is received through a closed conveyor system and taken to an enclosed storage area. From the storage area, the sawdust is carried to a dryer, where it is dried to a moisture content under 5%. The air in the dryer is heated using steam from the process. The annual sawdust consumption will be approximately 70,000 tonnes.
- From the dryer, the sawdust is sent via an intermediate storage area to the pyrolysis reactor. In the reactor, the sawdust is rapidly heated to around 500°C without any access to oxygen, creating the pyrolysis gas. The coke, the non-volatile part of the fuel, is separated from the pyrolysis gas and burned in a combustion chamber, while the remaining gas is piped off to a condenser.
- In the condenser, the pyrolysis gas cools into bio-oil. The bio-oil is purified before being pumped to the storage tank. The non-condensable gases are burned together with the coke in the combustion chamber.
- The flue gases from the combustion chamber are used for the production of steam. Some of the steam produced is used to preheat the air for the sawdust dryer and the excess is passed back to the sawmill and used in its drying kilns. The flue gases from the combustion chamber are cleaned in a dust separator before heading up the chimney.
The plant has been designed around a fast pyrolysis concept. Annual production of pyrolysis oil will total around 25,000 tonnes.
Pyrolysis oil
Pyrolysis oil is a dark brown liquid with a strong and slightly smoky odour and a low pH value. According to the CLP Regulation, which contains rules on the classification, labelling and packaging of chemical products, the oil is not classified as flammable or hazardous to the environment.
Pyrolysis oil can be used to replace fossil oil, for example in heating boilers in the energy sector and in industry more widely. It can also be used as raw material in chemical manufacturing or, as in the case of Pyrocell, to produce biofuels, which will play a significant role in the transition to a fossil-free transport sector.
Sale of Pyrolysis oil
Pyrocell offers sale of test volumes for those who want to try our bio-oil.
Order here >